A Better Way
Healthcare facilities are looking for ways to identify their surgical devices. There are instrument tracking programs that require laser etching for each instrument on site. As a manufacturer, we understand the risks of marking devices after they are manufactured. According to the NIH, current surgical instrument labeling techniques may increase the risk of unintentionally retained foreign objects. We understand that the Joint Commission has started citing facilities for using instruments that have been laser etched. The issue is that the laser etching process happens after the instrument is passivated, which creates a place for corrosion to develop. This presents a serious problem for the various tracking and inventory programs that use instrument level tracking and put their mark on after the product has been manufactured and passivated. Then, there is the Case Medical way: by tracking the instrument set and developing software for identification.
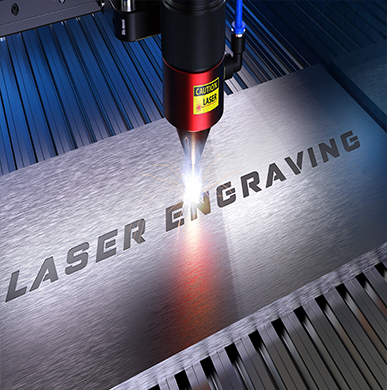
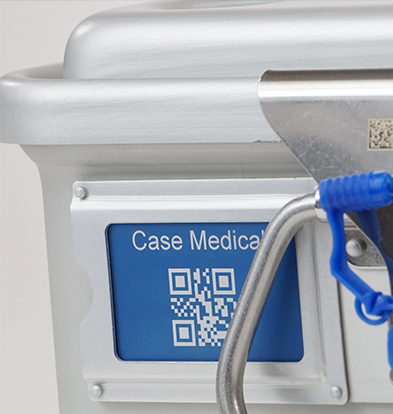
Avoiding A "Never Event"
While some may believe marking of surgical instruments is essential to ensure their proper identification, there are better ways. Those that are marked beforehand and passivated afterward have a protective, passive seal that prevents corrosion. We can't say the same for devices that are etched after the fact. The National Quality Forum defines unintentionally retained foreign objects in a surgical patient as a serious reportable event also called "never event." The best way to avoid damaging your instruments with laser etching is to not etch them at all after they have been manufactured and passivated. Case Medical can supply you with external ID plaques that are laser marked with a barocde, sealed after marking for surface integrity.
Tray Level Tracking Is Better
Tray level tracking allows you to manage your instrumentation without the tedious method of individually scanning each and every device in the tray. The external barcode on the container will provide access to the instrument list and photos of the contents and the inner tray, so you can move away from instrument level tracking to a more productive and easy to use system. Case Medical's proprietary ID plaques can be coded to work with an existing tracking system or link directly to Case Medical's state-of-the-art CaseTrak360 software. With CaseTrak360, the history of a set can be tracked in real time and can provide reports with a simple scan including how a set was used, how it was reprocessed, what sterilization cycles to select, how it was stored, all without patient data and without breaking the passive seal of the instrument.
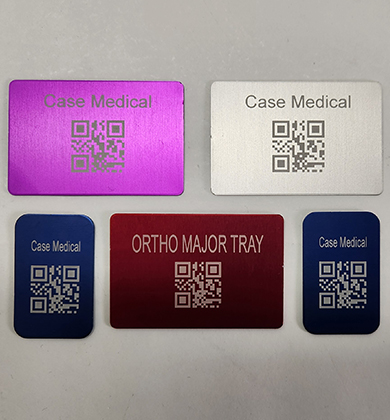
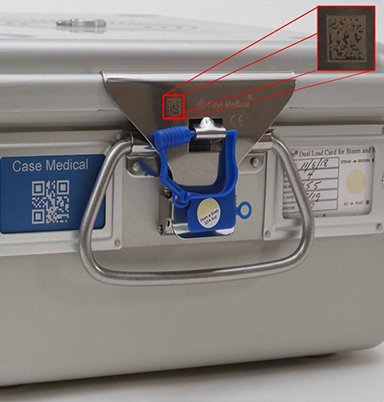
Data Visualization and the Full 360
Case Medical’s SteriTite containers come with a UDI barcode, laser etched or marked. This feature enables the user to access the human readable barcode and the IFU in 37 languages with a simple scan. Furthermore, request an ID plaqye from Case Medial with a feature we refer to as “digital visualization”. Digital visualization allows users of CaseTrak360 to instantly bring up set information, pictures, videos, count sheets, and reduce errors with encoded set comparison technology. Take a picture of the assembled set, download into the CaseTrak360 database. Use the software to compare the ideal configuration with the current assembly. You don't have to do the inspection, CaseTrak will do it for you.
Connect with Case Medical on social media for more content!
LinkedIn
FaceBook
Visit us anytime at www.casemed.com to learn more about our products and services. We are here to help. Case Medical is a U.S. EPA Safer Choice Partner of the Year and a Frontrunner in the Chemical Footprint Project. Contact us today to learn more about our certified eco-friendly cleaners and detergents and how we can help your facility’s bottom line with reusable and environmentally preferred products and services.
Kindest Regards,
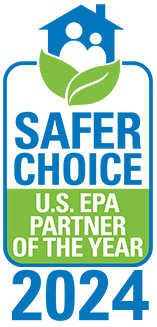